Waste Processing Products
Plasmothermic technology is designed to eliminate any degree of danger from solid industrial and domestic waste. Its application enables the burning components of waste to be burned, moving them into a gas phase and discharging an inorganic part of the waste. The waste gases shall be incinerated in the incinerator ' s vortex and shall be refrigerated and double-staded in the central-pine absorbers. In absorbers, the solution of the calysal clicks, the capture of dust and mild salts of metals. The dust and salts shall be accumulated as a sludge not exceeding 1 per cent of the mass of the waste being processed and then removed for burial or further processing. The purified gas shall be heated to 200 °C and released to the atmosphere. The content of harmful impurities (NOx, SOx, dust, carbon dioxide and furan hydrocarbons) in waste gases does not exceed EEC sanitary standards. The molten inorganic part of the waste is discharged into a water granuller and can be used as a construction material as a stowed chemically inert. Two types of plastic installations have been developed and tested.
(a) Plasmothermic installation for disposal of complex morphological and chemical waste.
Technical characteristics of the installation:
Waste production, kg/h 250 Plasmotron installed power, kW 150 Driving air flow, nm3/h 2400 compressed air flow rate, nm3/h, max 100 Waste gas volume, nm3/h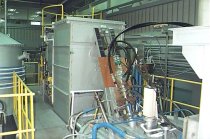
(b) Plasmotermical unit for the alloy of spider-type ash from fire-fighting installations
Plasmotermical unit for the melting of small-scale waste with a capacity of 1 MW (plasmotron vision)Main characteristics of the installation:
Waste production, kg/h 600 Power, MW 1 Temperature, oC in a floating chamber 1350 - 1400 incinerator 1,000 - 1100 Off-gas, nm3/h 1700 Electrical unit costs, kWh/kg 0, 8 - 1 Area occupied, m2 200Technological and economic benefits
- Reduce CO2 emissions;
- Ensure almost 100 per cent of hydrocarbon and carbon combustion;
- Transfer an inorganic part of the waste in one technology cycle into a chemically inert slag;
- Ensure the high environmental safety of waste products. At least 99 per cent of the volume of secondary products corresponds Sanitation standards EEC.
Related posts: